HydroX 2.0 (2023)

HydroX 2.0 utilizes an eight thruster configuration in order to allow for optimized travel in six degrees of freedom. Additionally, HydroX 2.0 utilizes the Qualcomm RB5 companion computer for path planning, thruster control, and vision processing.
SOFTWARE ARCHITECTURE
Using groundbreaking perception-enabled sensor technology, the Autono car is a fully driverless vehicle engineered to the highest degree of precision and safety. It’s autonomous driving reimagined.

Qualcomm RB5
The RB5 controls independent software stacks running on the vision processing system and ESCs, while the microprocessor on the 4-in-1 ESCs runs the BLHeli32 firmware for motor rotation settings and current limiting. The ESCs, communicating with the RB5 over a 2-wire interface, support the DSHOT protocol, enabling telemetry data retrieval. Additionally, the RB5 utilizes compass readings for accurate attitude control from external sensors such as the PNI RM3100.
PX4 FIRMWARE
The customized PX4 firmware, running on the RB5, incorporates custom airframe and actuator settings to accommodate the unique propulsion system of the HydroX 2.0. Compass readings from the PNI RM3100 are utilized for accurate attitude control, while external sensors connected via I2C and TCP are identified by drivers in the PX4 software, including two RAKwireless LX200V30 boards equipped with Qualcomm QCA7420 for decoding ethernet data over long distances.
MECHANICAL SYSTEMS
To expedite development, we utilized an off-the-shelf enclosure and frame structure from Blue Robotics. After evaluating the mission requirements, we determined that an 8-thruster configuration was optimal, enhancing maneuverability in the z-axis and pitching/rolling. By angling four thrusters towards the middle of HydroX 2.0, we enabled movement in the x-y plane without physically rotating the robot, conserving battery power and increasing efficiency.
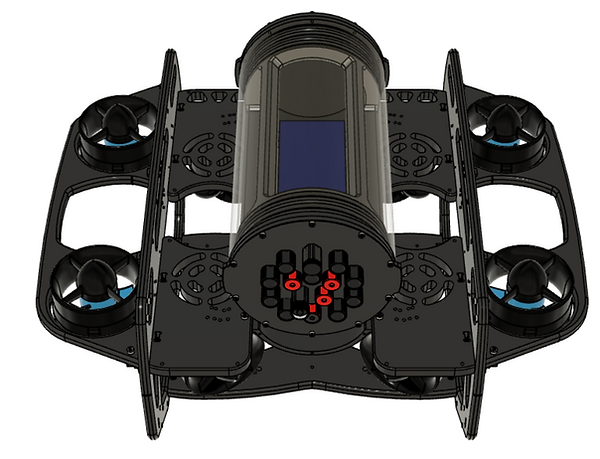
3D PRINTED ENCLOSURE
We utilized a waterproof cylindrical enclosure with a 6-inch diameter and 11.75-inch length, featuring a watertight seal using pressed fit o-rings. To maximize space, we iteratively designed and 3D printed mounting systems for our electronics, resulting in a modular and user-friendly design. The enclosure structure, made of ABS, consists of a cylindrical piece and a connector lid, allowing easy removal of all electronics as a single unit. Additionally, the hardware was strategically positioned for convenient access to connectors and power sources.
TETHER TOP BOX
We designed a tether box to house the RAKwireless LX200V30 that allows us to communicate to the AUV through an ethernet cable. The box is 3D printed with ABS to be able to withstand outdoor use, and stay durable overtime. The seal is printed with TPU, a flexible filament that is able to stretch and compress, allowing us to create a watertight seal between the body and the lid.
